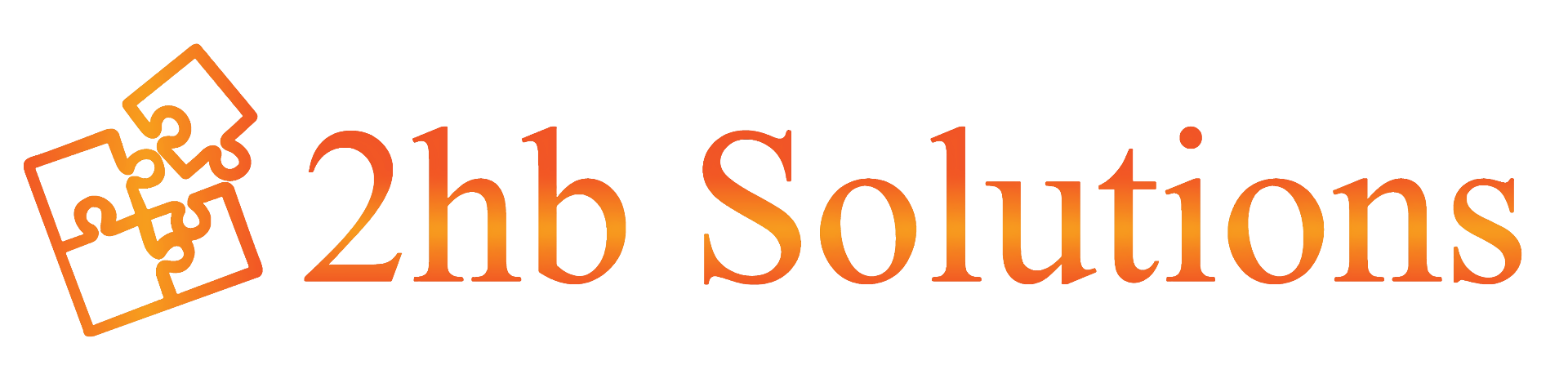
**Maintenance Contracting & Support**
Shift Cover, Recruitment infill
Preventative Maintenance, Continuous Improvement
Problem Solving, RCA, DoE's, FMEA ......
Introduction / Summary ....
I'm an experienced Maintenance Engineer, particularly good at fault finding and solving machine problems, to OEM, or with improvements to prevent reoccurrence.Maybe, your head count is capped but you're able to use a contractor?Maybe, there is one issue that requires time you don't have?You may have a team of Maintenance people, or are running a factory by yourself.When you're looking for reliable, quality help, to add value, with no headaches, please call for a chat.I'm open to a variety of contracts, let me know what YOU need.
Thank you for your time and I hope to meet you in the near future - Chris iles.
Production Support, Shutdowns, Design & Build, Pimp my machine (upgrade an old faithful), .....
*Photo - double glazing internal spacer making machine - Clayton South
More about 2hb
When things aren't running 'just right', it can be hard to know where to turn and who can help.I've been solving Machine & Automation problems for the last 25 years. I'd love to see the challenges you face, introduce myself and let you know where and how I can assist.Click the 'i' button below for more information.
*Photo taken at McClelland Sculpture Park by my daughter
Machinery
Rarely does one size fit all.....
What do you want your machine to do?
Continuous improvement, modifications, ...
*Photo - one morning leaving home for work
Processes
Production & Maintenance
Procedures, documentation, compliance ...
*Photo - High speed through a tunnel - stock image
World Class Maunufacturing
Reliability, TPM, ...
*Photo - Thinking outside of the box - stock image
Get Notified
To start a project or for more information, please forward your details using this form or use the quick email link button below to easily send me details, or call
Chris 042 393 8855
© 2hb. All rights reserved. Special thanks goes to all the great people I have worked with over the years, only some of them are mentioned here; John Williams, Lewis Hook. James Burgess, Craig Brice, Miles Gorgioski, & Neil Roos. Please forward any website suggestions to [email protected]. Thank you.
Time for a quick chat?
Simply email or call me to arrange a visit at a time of your convenience.The most important thing is what YOU would like YOUR machinery to do?I really like efficiencies, simplicity, and utilization... I also love a challenge.
Many projects, when looked at in hindsight, seem very simplistic, but each problem presents itself in different ways and is often hidden behind a number of consequential symptoms. How often have we (all) kicked ourselves after discovering the problem was !!!! That's the beauty of a solved problem :-)
*For an example of a project I was heavily involved in, below is a simplified story of the evolution of a high speed machine that produced tiny precision metal components at 3 parts a second, worked 20hrs/day and we had eleven of them.For a quick overview, click here (or below link), for the longer story, please read on...
This was a great collaboration between Maintenance & Production that resolved a number of issues, as below;Issue 1: Intermittent jams
Issue 2: 1 in 1,000 bad parts in delivery
Issue 3: Over supply (to ensure meeting order)
Issue 4: Minor stops affecting production figures
Issue 4: Variation between machines (6 in UK, 5 in Malaysia)
Issue 5: Difficult, lengthy set-ups, often requiring specific operators
The main cause of the intermittent jams was associated with knife wear, so a change out schedule was implemented and a study into better knives was started however, when the machine did fault it took considerable time to clear and required the whole process of setting up to be reperformed.By monitoring the output, we were able to conditionally stop the machine at the first instance, preventing the jam, catch out of spec parts and prevent the lengthy set-up.This was achieved with program code and a pneumatic flap added to the outlet chute. This in turn addressed one instance of issue two, bad parts contaminating a good parts tub.For the second instance of bad parts, we knew the first parts were out of spec as the machine ran up to speed. We introduced a colour sensor to the the product tub conveyor and coded it into the start code, preventing start until a Red scrap bin was placed under the chute. We then added further code to automatically move the conveyor after a set number of 'start-up' cycles.The Oversupply, was due to difficulties sensing a randomly spinning, shiny object (the size of a small pea), being made in 30mS, ejected from the machine with an air knife.We could detect it ok, but it would occasionally be detected twice, and with batch sizes in the ten thousand bracket and sequential orders in the millions of parts bracket, the solution for a number of years had been accurate weighing, plus an error margin oversupply.We had previously trialed numerous sensors, but none surpassed the great one we were using. They either had the same occasional double count, or weren't sensitive enough and missed parts.Thinking outside of the box, I combined the just written bad part monitoring code with a rising edge count using the TDC sensor.This achieved a 99.9% accurate count, saved significant $$ and addressed a customer complaint regarding the oversupply. For context, the UK plant alone, produced 1.5 million parts per day! (Malaysia produced around 1million parts/day)The Reduction of minimal stops had already been impacted by reducing jams, but a number of other contenders were now addressed.A free spinning spindle (used to curl the rings) was made up of a number of bearings contained within a tube, that attached to a reciprocal cam. The actual spindle size was only a few millimeters in diameter. The spindle located into a further bearing before being spun with a servo driven, rubberised 'curling wheel'.The replacement of the bearings within the tube assembly took about 20 minutes. Add in time to get the new parts, etc. etc. the whole repair was around 30 mins.By making an extra ready made up sub-assembly, the operators could now change out the whole part in seconds. (No waiting for maintenance, very minimal downtime and the worn assembly could be serviced whilst production continued, without stress, and returned to the machine for reuse when required. With further monitoring of the typical MTBF's, we chose an appropriate cycle life of the bearings, and this was also added to the program, flashing a warning for change, prior to failure.Next, a depth sensor was added to the infeed spool.With the addition of some further code, I could flash an orange screen on the HMI with clear, big text, alerting the operator, to prepare & splice a new spool, and monitor the change over, utilising the scrap bin, keeping the machine running.Limiting variation was very important to us. Certain machines were better at different product runs.Each machine was built the same, but minor differences in sensor position for instance, changed them each slightly. There were about five different sensors, responsible for different parts of the process. It was near impossible to get these aligned the same in each machineWe addressed this by utilising a cam positioner and 720 encoder. We could now set every machine identically (digitally), instantly, shortening the lengthy technical set up and removing the slight variation between machines. This was a game changer which also simplified technical support to our other plant and addressed part of;Issue 5 Difficult, lengthy set-up.The internal 5 ton press was the focus next. It used a basic strain gauge with rudimentary electronics, was prone to 'drift' and was affected by heat (which we address further down). This set-up was not especially accurate and was another cause of variation between machines, complicated initial set-up and limited fine control.We made a test rig, and placed four miniature piezo electric load cells into it. These were very accurate and when coupled with an electronics controller designed for high speed plastic injection molding, was able to capture the whole force curve, overlay it on top of previous curves and monitor the whole process in really fine, repeatable, accurate detail.(Now, bear in mind, as mobile phones evolve for instance, we're impressed by less each and every year. At this time, Apple had just released the I-phone 3!Having been used to getting a sketchy, 'do I even trust this measurement' from the strain gauge, to all of a sudden be able to study the whole force curve, was a significant leap)Using this test rig, we could accurately set each machine making fine adjustments to balance each press, centering force evenly (one cause of excessive heat).A further benefit of our new set-up, was the ability to use pass / fail monitoring of every part and stop the machine within conditional limits.The data captured helped us develop the machine further than we'd imagined.Each issue was addressed in the order of importance with some development being worked on simultaneously, whilst tooling was prepared or whilst awaiting parts. We worked as a team, utilised RCA and other LEAN tools, gaining approvals at each stage.Once I had deciphered the PLC program (written in Italian) and laden with Function blocks, it was relatively straight forward adding the new code, although some out of box thinking was required at times!The electronics and software supporting the piezo-electric load cells was top notch, able to work so accurately at such high speed. I'd use the same manufacturer of this equipment in a heartbeat.Yet another modification was to fully understand and maximise the proportional lubrication system. This had never been perfected, but now, with such good results and cost savings, it rose to the fore.With the machine running so well, there appeared two scenarios. We seemed to have either overheating or oil contamination. The latter wasn't so much of an issue, as the components had further processing that removed any fine traces present. Previously, the main cause of overheating was excessive force applied by the press ( this was due to uneven tooling, which we'd addressed above).The task was straight forward enough, fit the right nozzles in the right areas and fine tune the dosing.When looking at the fine tuning of the dosing, it was imperative to be able to easily adjust the settings whilst in production mode. A simple addition to the HMI screen and more coding, made this possible. Whilst I was there, I translated Italian or strange translated error messages to ones that made sense to all the operators. Also, why not utilise the colour function of the HMI's too? So, a red background was used for important errors, orange for minor alerts and green when normal.Hold the phone! Why not also add in some helpful fields to display on the home-screen, like machine temperature AND, why not add in password protection to some variables, and limits to others? We did all this, as well as increasing font sizes, standardising all eleven displays and upgrading some older variants so all the machines were the same and any operator could comfortably use and switch between any of them.A small improvement? In comparrison to the other advances, yes, but which do you think made the staff the happiest (including the maintenance team)?There's more! (but enough already!)Let's just say we continued in this fashion, addressing the next highest concern, suggestion or idea, The savings were huge, the quality had increased, the downtime minimised and minor stops were all but non existent.With each improvement, we gained more time to work on the next, and as maintenance intervention was becoming so minimal, we had time to address the other types of machines we had and we made similar successes there too.The company had set-up a very, very good environment for this Continuous Improvement program and shared its successes with the staff, fueling the fire to continue. The company was the leader of continuous improvement in the whole group, consistently for many years. It was a pleasure to work in such an environment. I learnt a great deal through the experience and would gladly share the insights gained if you wish to know more.
-**Imagine doing business a little differently and a host of opportunity can open up. **
As the saying goes, "There's more than one way to skin a cat"Here's a less intense, but very effective mod;Have a look at the labels on the photo below; For some other examples - please look hereThis was such a simple modification (with only some code alteration), but it saved thousands of dollars from incorrect product picking and faster processing.Both labels have the same info, but some simple changes were made.
- Simple label colours for certain products
- Important text readable from the forklift
- Automatic label details from simple, already used codes - three letters and all the other relevant data was added automaticallyEven the gatehouse could check loads against orders quickly and effectively by a simple glance instead of the detailed examination the old label demanded - (KISS - Keep It Simple, Stupid! )This is just to illustrate how simple a solution can be - it just needs someone to spot it and do it!The Yellow label is the new version and has the production date in the largest font we could fit in the space available (which I maximised by reoganising the layout of the old label). The three letter code (YEB) is the style and colour code used by the manufacturer and was now the only input required by operators to initiate printing for the current production run, all other details like production date, production shift and batch code were all automatically added by code in the background.Prior to this simple modification, mistakes had been made with significant costs incurred to rectify incorrect deliveries. Further inconvenience from incorrect 'picking' of product complicated the FIFO stock rotation to the point that we spent two months reorganising over three million concrete roof tiles into an ordered and organised yard with high moving product lines closest to the production outfeed, minimising fork lift movements dramatically, increasing efficiency in the stock yard as well!It is amazing, how much affect a simple change can make. In this instance, the reorganisation of the stock yard was a big undertaking, yet the changes to the label and the ease of creating a correct, easy to read label, were very simple and very effective.
Now the ease of stock taking, the ease of storing production runs, the increased speed of loading trucks (correctly) are savings that will be enjoyed for a long, long time.
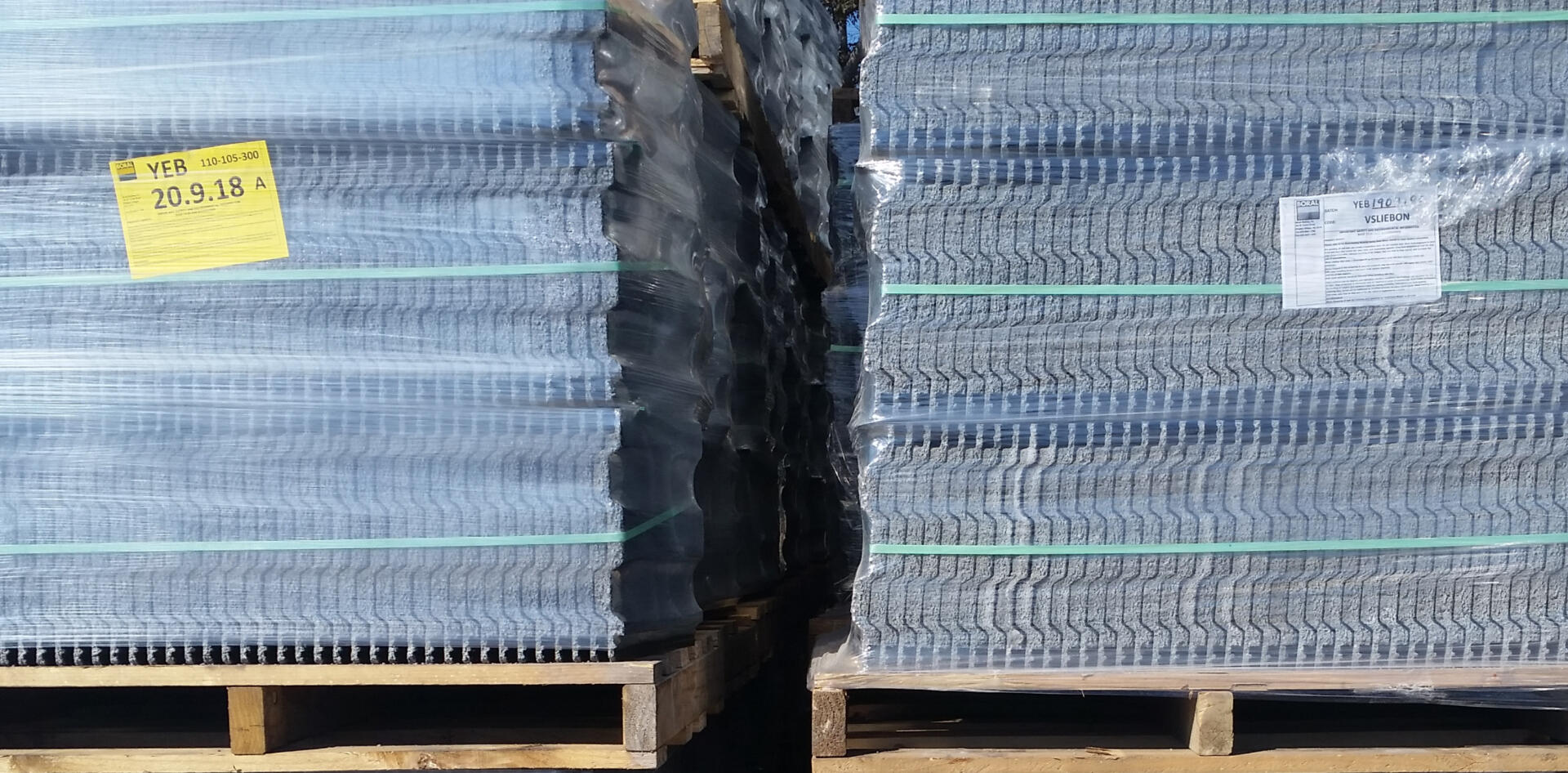
*Background picture taken in Montague orchard, Narre Warren
*Label picture taken in Springvale
Machine improvements
For inspiration, here's some examples of some completed projects;
*An example project I was heavily involved in, is the 'evolution' of a high speed machine that produced tiny precision metal components. For the longer story, click here, for the quick overview please read on...
-Accurate Counting: This particular tiny, spinning, shiny product is made in fractions of a second. Because of these properties, regardless of sensors used, false counts were commonplace BEFORE this modification. (saving $100k/pa)
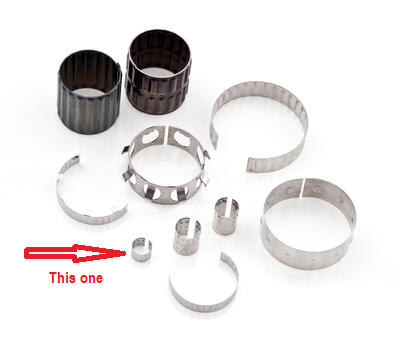
-Accurate positioning: to half a degree. (This modification brought the machine up to WCM standards and facilitated all eleven machines to be timed precisely, allowing total flexibility without concern
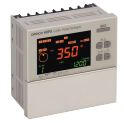
-High Speed Press Monitoring: at 3parts/sec, a full force curve display with pass / fail monitoring and control.
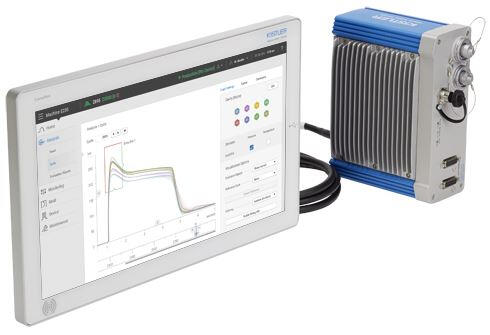
-Improved HMI's: -Error messages that made sense and utilising the features of the screens we were already using ( like changing colour to bright orange & large text when displaying errors, password protecting critical adjustments, & the 'Home' Screen displaying desired info like machine temperature, speed, etc. - this simple modification of the existing screens really helped the operators, increased efficiencies AND moral significantly.
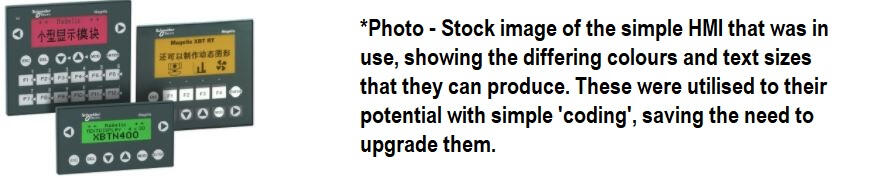
-Automatic Proportional Lubrication: timed to tenth/sec from HMI, password protected. Eliminated overheating / contamination trade off increasing uptime, minimising damage.-Sub Assemblies: reducing change over times from thirty minutes to one minute #SMED-Sound reductions: to the order of 50%, saving the need to wear hearing protection PPE.-Low material pre-warning: alerting the operator prior, eliminating minor stops.-Conditional Start: Preventing machine starting unless certain conditions met - in this case, a RED product (scrap) bin as the first few pieces were known to be out of spec.-Conditional Auto Stop: - if a part wasn't ejected, the part before it was likely to be out of spec - so we caught it! - plus we stopped the machine prior to a fatal jam minimising wastage and serious downtime
Some of the solutions were straight forward, others had challenges that couldn't be overcome before. Most solutions came from excellent communication, teamwork and tenacity. The savings were huge and costs returned within months. All the improvements were trialed and tested on one machine before being rolled out to all eleven, five of which were in Malaysia. I would often ship everything required before flying to Malaysia to modify the machines, train the staff, leave spares, instructions and provide telephone support when needed.There are too many examples to list all the Continuous Improvements I have been involved with and often, when looked at in hindsight, seem obvious and simple, and whilst some were, the improvement for Production ranged from 'Brilliant!' to 'Fantastic !!' - well worth the effort.
*Photo - Part of an Italian wire bending machine that has been converted to high speed production of high tolerance, stainless steel components - Bristol & Malaysia
Process
From completing an FMEA on a critical asset to identifying every step of a production process, good documentation can be goldust - often seen as too involved when there's so much else to do! Getting some of those gems down though, can be quick and very worthwhile ...
- Value Stream Mapping - what's important -makes the money, and what isn't!
- Reduced Set-up times - SMED
- Asset Management - What to do and WhenFMEA - Failure Mode Event Analysis - A simple look at what can go wrong and how to be prepared for it
RCA - Root Cause Analysis - What did go wrong and how to get out of it
Autonomous Maintenance - How to get things done more fluidlyCompliance
Operator asset care & TPM
Mistake Proofing - PokayokeEmployee Engagement
How to free-up time for improvements
Kanban & JIT - Just in TimeCMMS - Computerized Maintenance Management Systems
KPI in Maintenance
Reliability Centered MaintenanceIndustry 4.0
Ideal Production Pace (takt)
Theory of Constraints (TOC)Preventative Maintenance
MTBF and MTTR
Maintenance Structure & Procedures5s
Waste reduction
OEE
Design of Experiments
SCRUM's
*Photo - part of a pyrolysis kiln - Dandenong South
World Class Manufacturing
World Class Manufacturing (WCM) is a mindset based on a continuous improvement approach.WCM has its foundations in the Total Productive Maintenance (TPM), a maintenance process, making processes more reliable & less wasteful.It has extremely high goals that can inspire and motivate teams if approached correctly.Why LEAN Manufacturing gets Bad & Good reviews - What goes wrong?You may have heard, or experienced many things around LEAN manufacturing, that has put you off adopting any of it, which would be understandable from some of the things I have seen and stories I've heard. I have however, been very fortunate to experience some companies that got it right.I believe some of it can be adopted easily, with little fuss, no upheaval, minimal cost and with high returns.Please ask me about how easy adopting some WCM habits are and how effective they can be at raising employee engagement when managed well.
► Motivating environment, engaged staff - this is massive! And possibly, enough reason on its own to have a chat about the bits that work.
► High level of transparency - this one scares people the most!
► People are the driving force of change - sharing the load - not one or two, but many super heros!
► Continuous improvement through loss eradication - make the things that need it, better!
► Zero accidents, zero breakdowns, zero defects, zero scrap Possible???!!
► No type of waste is accepted - duh! - but there's a bit to this one worth chatting about
► Methods for improvements are applied using WCM procedure - changes aren't made all over the place without a sense check!
► Voice of customer is heard to the last level in the organization - Even the work experience kid can get involved! Often the best assets of a company, its staff, can be overlooked and steamrollered by over zealous busy bodies! - there are ways to prevent this and help people help YOU!
*Photo - apples transferring to the 'grader' after having been scanned - Narre Warren
Employee Engagement
I have been surprised how many other departments are affected by the Maintenance Department and how the outlook of each of the Maintenance Crew can lift or lower moral.Maintenance really is the place to start when you want engaged staff throughout your factory. Support and help the Maintenance Department evolve and it will pay dividends back tenfold.There's too much to write here, but these guys are diamonds....
► Motivating environment, engaged staff - this is massive! And possibly, enough reason on its own to have a chat about the bits that work.
*Photo - an amazingly straight tree pic I took in NZ
About
I'm insatiably curious. I love figuring out how machines, situations and objects work, and how they could work better: faster, smarter, deeper, with quality results.I'm a lateral thinker, organiser and problem solver.Whatever your machinery / automation needs, I would be pleased to come out to see you.For an example of my work, please click here for the long story, or for the highlights, click hereChris - 042 393 8855
*Photo - Kawarau bridge bungee jump in Queenstown, NZ - loved it! (full pic on desktop site)
Thank you
Mobile# 042 393 88555We will be in touch soon